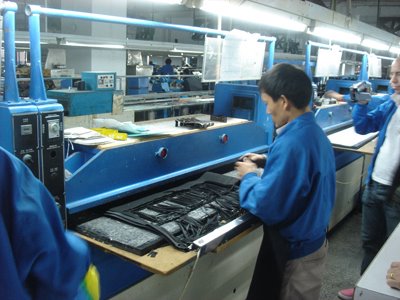
The next step in production is cutting and preparation.
In this stage, the selected materials are taken from the material warehouse, and brought to the cutting room or area. Cutting dies are used, which are metal cookies cutter like dies, used with a large stamping machine that puts puses down the die onto the material.
More info and pics after the Ream More link below

See cutting machine pics above. Depending on the material, these cutting dies and machines can cut through more than layer of material at a time. For materials like collar lining foams, reinforcements, and synthetics, they typically cut 3-5 layers of material at once. For leathers, because they stretch and the materials is very costly if wasted, the operators cut one layer at a time. The boards on the cutting machines are layered in a thick wax block, to keep the dies sharp and ensure good, clean cuts every time.

As mentioned earlier, care is taken throught the cutting process to minimize waste and nest the part layout to maximize material use. In some cases, this layout of how the cut parts should be taken from a piece of material, is planned by a special computer program. Different materials also have different concerns and waste in cutting. For example, because of the nature of the skin and animal, Goat Skin Leather has a much lower loss rate than Kangaroo leather (and the raw skin is also bigger). This not only affects the cost of a material on a boot, but also effects the result of final product.

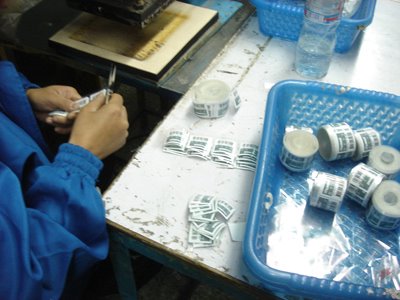
During cutting, especially of leather, becuase the natural material may vary in grain texture and color, small stickers are put on the cut parts, to ensure that the part for the left and right shoe in one pair come from the same material for best consistency.

After cuttting, parts may be screen printed with stitching guidelines as shown above with special inks that will disappear or be only visible in UV light, to help stitching workers follow the necessary stitching lines on a pattern. This is especially important for decoration stitching that must be in certain pattern like the vamp stitching on the vamp of the 4.2 Concept as shown above.


It is also during this step, that the edges of materials (both leather and synthetic) are made thinner to have a better looking seams and avoid unsightly bulges. This process is called skiving. This is done as shown above with a special machine that will cut the thickness of the leather down using a special spining blade. Skiving may typically reduce leather material thickness from something like 1.2mm to 0.5mm

Materials
Cutting
Printing and HF embossing
Stitching
Lasting
Assembly
final QC and packing
Labels: case study, china, design, development, factory, football, hummel, leather, materials, process, production
1 Comments:
actually thats a perfect analogy and the spinning blad i mentioned is similar to one on a wood router.
Post a Comment
<< Home